Frequently Asked Questions
The main causes of problems in the application of product to various components are:
- Inclusions
- Poor cleaning
- Silicone contamination
- Poor spraying techniques
- Poor handling.
These may all be generally eliminated by careful attention to detail, tight quality control inspection procedures and by thorough and regular housekeeping. A schedule of equipment maintenance and inspection should be laid down and this should be closely adhered to, to minimise downtime. Some points to note here are to ensure that the components are thoroughly prepared and that the incoming air to the booth is properly filtered. These will eliminate most of the problems, although a few vital pointers are given below.
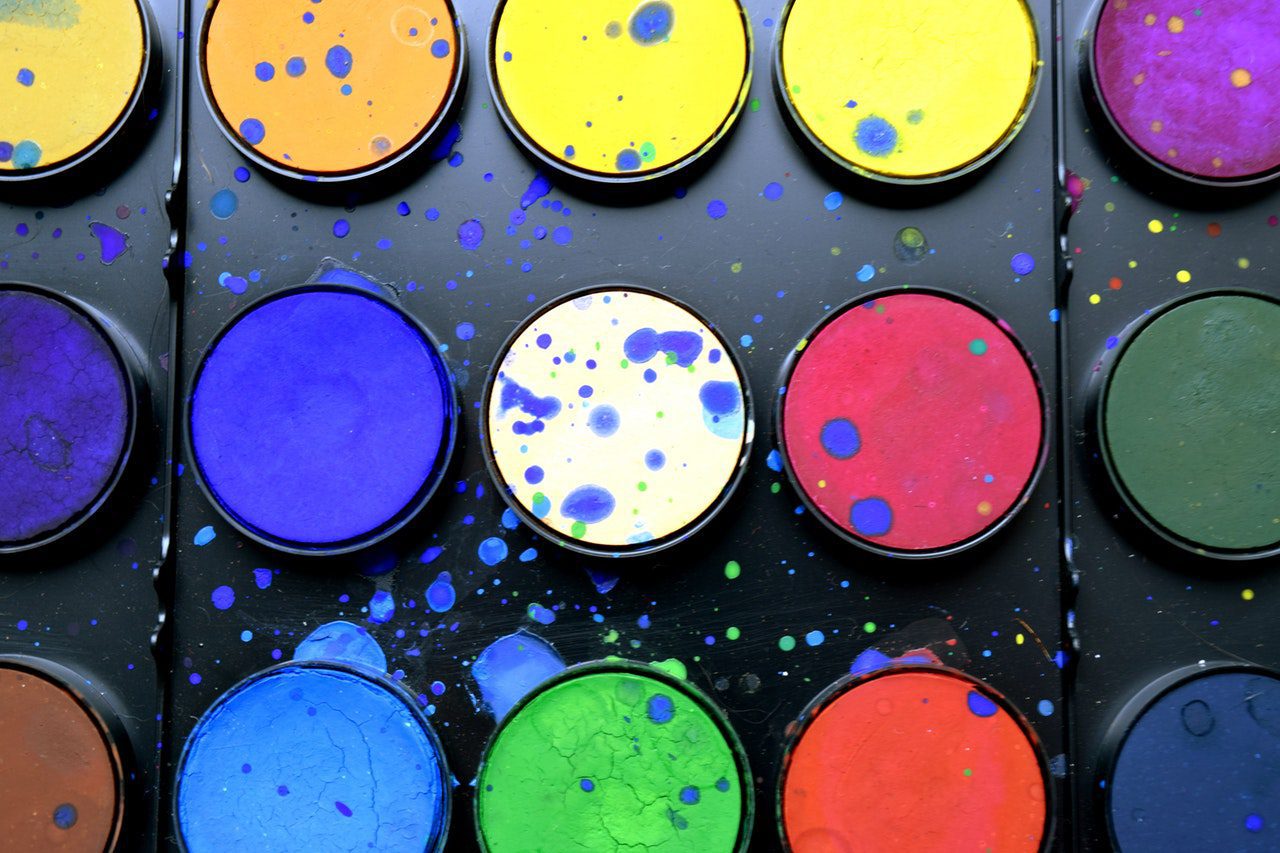
Spray Techniques
a) Runs
Cause: Too much product
Solution: Apply a lighter coat
b) Orange Peel
Cause 1: Slightly too much product
Solution 1: Re-adjust gun set up
Cause 2: Product too thick
Solution 2: Check viscosity – if lid has been left off, product will thicken, use Avkote 95 Thinner to thin to a maximum of 10% by weight.
c) Solvent Popping
Cause 1: Too much product applied too quickly
Solution 1: Apply a lighter coat
Cause 2: Too much heat applied too quickly
Solution 2: Adjust heat control
d) Inclusions
Cause 1: Booth filters too dirty
Solution 1: Change or clean filters
Cause 2: Grease, etc in airlines
Solution 2: Check seals on compressor and ensure airline filters are functioning properly
Cause 3: Particles in product
Solution 3: All paint should be filtered before use
Extending Drying times
Generally between 5% and 10% (by weight) of thinners should be added in order to lengthen the drying time. However, not more than 10% thinner should be added to any colour, as this will increase the drying time excessively. We recommend Avkote Thinners 550 but please contact us for more specific information.
Poor Adhesion
In order to obtain good adhesion when spraying, vigorous cleaning with Avkote 153b with 154 cleaner or double cleaning will be necessary to remove waxes, which have migrated to the surface. When this problem is encountered it is advisable to find out the date the profile was produced. If coating is carried out immediately after extrusion some of the agents may still be released from the plastic. It is possible to gain good adhesion, even with these agents, if the substrate is scotched first before cleaning with Avkote 153b with 154 cleaner.
What are the terms and conditions?
All are available on the Terms & Conditions page.
Static Removal
As PVC-u is an insulator it is important to eliminate static as this will attract small particles and subsequently cause small surface defects. A clean environment with properly filtered inlet air and positive pressure will eliminate a great proportion of the particles attracted by static. Lint free rags should be used to wipe the surface before the use of the air curtain.
Cleaning/Silicone Contamination on Plastics
a) Spray Equipment
All spray equipment must be cleaned regularly and this can be done with most proprietary gun cleaning solvents for example Standard Thinners. Ensure care is taken when using these products as they can seriously affect PVC-u.
The guns and pots must be cleaned as required between colours proprietary gun cleaning apparatus and should not be allowed to stand for extended periods as this will cause problems and reduce the lift of both the equipment and the product.
b) Degreasing
This should be carried out prior to spraying to remove materials such as grease and dirt, which can originate at the point of extrusion from the PVC-u. Small quantities may be cleaned by hand or high-pressure washer after removal of protective film.
c) Silicone Removal
Silicone removal is essential prior to spraying and there are a number of recommendations for removing and minimising silicone related problems and these should be following carefully. Silicones are used widely in the PVC-u industry for window and gasket installation, which is why this problem is highlighted. As prevention is better than cure, the best method of overcoming this problem is to ensure that no silicones are allowed in the plant. Although this is not always practical, all components should be tested for silicone contamination. There are a number of means for removing silicones and these should be stringently applied where any evidence of silicones is obvious. The use of a quality degreasing solution, Avkote 153b with 154 cleaner, will remove small quantities of silicones, but large-scale removal is difficult.